CORRUGATED CARDBOARD |
 |
Though most people rarely give it a passing thought, cardboard is a nearly essential part of our day to day society. Produce, canned goods, and packaged foods are shipped and received on sturdy cardboard flats and boxes, without which there would be utter disarray in transport and storage.
Self-assembled furniture such as bookshelves and kitchen tables would arrive scratched and broken if not for their protective cardboard barrier. And of course, your beautiful canvas prints and picture frames wouldn't be nearly as safe outside the boxes made to fit each and every order.
|
SUMMARY
There are many different thicknesses and styles of corrugated cardboard and the boxes into which it is formed.
Types |
Flutes |
Box Styles |
Tests |
- Single face
- Single wall
- Double wall
- Triple wall
|
- A flute
- B flute
- C flute
- E flute
- F flute
|
- Slotted
- Half Slotted
- Tray
- Full Overlap
- Roll End
|
- Edge Crush Test
- Burst Test
|
This article also discusses:
- Recycling and reusing corrugated cardboard
- KeenART Media's own use of corrugated cardboard
- Cardboard as an art form!
|
HISTORY OF CORRUGATED CARDBOARD
|
 |
While cardboard has a history that could be traced back to the second century, when the Chinese invented paper, the more recent invention of corrugated cardboard came about in the mid-nineteenth century in Britain, where it was patented for use within tall, stovepipe-style hats.
In 1871, an American industrialist patented his use of this corrugated cardboard to line the inside of boxes, thereby making them more difficult to crush, and able to be stacked higher.
A few years later, yet another innovator developed the idea of a double-sided corrugated cardboard, like the one we know today. Around this time, the idea for pre-fabricated cardboard boxes was developed - the kind that could be shipped flat with all necessary cuts and seams to be folded into a box when needed. In 1890, the first machine to manufacture pre-cut cardboard boxes were developed.
|
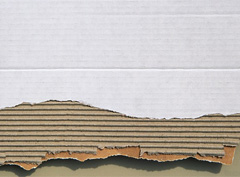 Corrugated cardboard
|
MAKING CORRUGATED CARDBOARD
|
 |
Corrugated cardboard is made up of three sheets of strong and lightweight, paper-based fiber called kraft paper. This paper, made from wood chips ground into pulp, was invented in 1884. Once this paper has been processed and loaded as large rolls, it is moved to the a corrugating plant, otherwise known as a converting plant.
The center sheet of kraft paper - the ridged or "fluted" one - passes through the belts and cylinders of a corrugating machine. This machine can be as long as 300 feet, depending on the capabilities of the manufacturer. As each roll of paper nears the end, a splicer connected the end of one roll to the start of another, creating a continuous process.
Once the center sheet has been fluted, it is adhered with a strong glue to the surface of another sheet - the flat linerboard that serves as the outer surface of the finished cardboard sheet. A second linerboard is glued to the other side of the fluted sheet, effectively containing the ridged piece and creating a very stable board that is difficult to bend at the length, but simple to fold within the ridges. This style is called "single wall" board.
Though it does not have the strength of cardboard with two linerboards, "single face" board is available, which has linerboard on only one side of the fluted material. This is commonly used for extra protection for packaged products, and is much cheaper to produce and buy.
FLUTE DESIGNATIONS
Corrugated cardboard sheets and boxes come in a variety of different, lettered grades, each with different weights they can withstand. Though each manufacturer may have slight variations (there is no strict standardization), the cardboard is graded based on the number of flutes (ridges) per linear foot, always allowing for plus/minus 3 or 4 flutes. An relatively uniform thickness (height of the flute arch) also applies to each grade, though measuring for flutes/linear foot is more reliable than measuring thickness to determine the grade.
It is significant to note that letterd grading was applied based on chronology of invention, not on increasing or decreasing size.
Flute Designation |
Flutes / Linear Foot |
Flute Thickness (inches) |
Common Use |
A-Flute |
33 |
3/16 |
Very thick - good for dividing stacks and providing cushioning |
B-Flute |
47 |
1/8 |
Useful for die-cutting and interior packing |
C-Flute |
39 |
5/32 |
Most common grade for custom boxes |
E-Flute |
90 |
1/16 |
Very thin - best for printing packaging that will be visible at point of purchase |
F-Flute |
128 |
1/32 |
The newest and thinnest - more sustainable for products requiring less protection |
BC-Flute |
86 |
9/32 |
The most common double-wall - for bulk bins and exterior shipping containers |
BE-Flute |
137 |
3/16 |
A thinner double-wall - useful for heavy duty packaging requiring printing |
(K-flute and N-flute corrugated cardboard is also available, but is not commonly used or manufactured.)
|
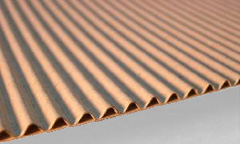
Single face corrugated cardboard
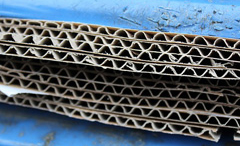
Single-wall corrugated cardboard
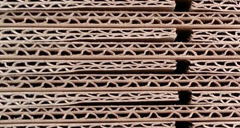
Double-wall corrugated cardboard
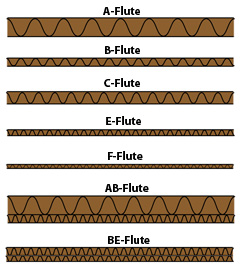
Corrugated cardboard flutes
|
CARDBOARD BOXES
|
 |
Most cardboard boxes sold today are corrugated. Even if they look very thin, they may be an E- or F-flute which, remember, is only 1/16 or 1/32 of an inch thick.
If sold in bulk, cardboard boxes are almost always shipped flat. This makes shipping easier for the manufacturer, and prevents the purchaser from requiring space to store hundreds of pre-formed boxes. Instead, they can simply construct boxes as they are needed.
Despite the seemingly easy process of ordering pre-cut, flattened boxes, there are in fact a great many different kinds of cardboard boxes available today, each one manufactured to suit a specific purpose.
Box Type |
Description |
Box Type |
Description |
Standard "Slotted" Box |
The most common type of box packaging used. These boxes are made from single wall cardboard, generally C flute, and may be adjustable, allowing the buyer to cut the folding flaps larger to lessen the box height. The top and bottom each feature four flaps the length of 1/2 the box width - one on each side. The two longer flats meet in the middle to provide a "lid." |
"Half Slotted" Standard Box |
These boxes are almost identical to a standard box, but do not have top flaps. By leaving one end open, the box can be placed over another box to serve as a lid (therefore doubling protection on the sides), or placed over large, heavy items than cannot easily be lifted out of a box, such as refrigerators. |
Full Overlap Box |
Instead of half-wide flaps, this box style features top and bottom flaps that reach all the way to the other side of the box. When closed, four layers of cardboard create a four-sheet thickness on the top and bottom of the box. This provides extra security for heavy items such as washing machines. |
Trays |
With short sides and generally no lid, these boxes are most often used as point-of-purchase packaging, which means the product will remain in the box while on the store shelf (soup, cat food, etc). The sides are created by folding over flaps and securing them in the base of the box, giving the sides double thickness and therefore extra stability. |
Long/Tall Box |
These boxes may have either full overlap or slotted flaps, but are very long and narrow, designed to hold tube-shaped items. The flaps are usually located on the long end, though they may open along the narrow end, to allow the item to be set in rather than slid. Due to their short depth and width, they are generally quite resistant to crushing. |
Roll End Box |
These boxes require no gluing - the sides fold over to be secured by slats in the bottom edges of the box, like the trays mentioned above. This gives these sides extra stability since they are doubled over. This type of box often has a lid as described in the die-cut box, attached at one side and tucked in or folded over the top of the box. |
Die-Cut Custom Box |
An example of this is a banker's box. Created to match the specifications of a certain customer, these boxes may be virtually any dimensions. They often include an attached lid with a lip that tucks into or secures over the side of the box, similar to a hinged lid on a wood box. They may be made with slightly thicker corrugated cardboard, such as B flute. |
Pillow Box |
Though these boxes are technically die cut to unique specifications, they receive a category of their own due to their unique shape. Pillow boxes fold in at each end on a curved crease, caused the unfolded sides to "puff" up. They are often used for novelties, to hold chocolates, party or wedding favors, or other delicate items. |
|
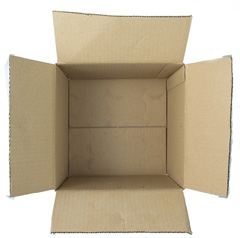
Standard slotted box
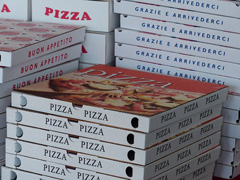
Die-cut, custom boxes
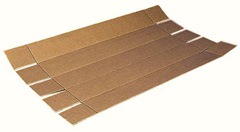
A long box unassembled
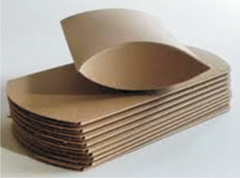
A pillow box
|
CARDBOARD BOX STRENGTH TESTS
|
 |
In addition to the flute measurements, corrugated cardboard is subjected to tests to determine how much weight it can bear.
Edge Crush Test
This test measures how well a box made from a given grade of cardboard will stand up to stacking. As the name suggests, a finished box has increasing pressure applied to its vertical side until it crushes. This test gives the box an ECT rating. ECT 32 (or EC 32) is a common rating which means the box can withstand 32 pounds per square inch before crushing. Knowing this rating, the buyer can determine how many boxes they can safely stack on top of one another, depending on the weight of the product.
Burst Test
The amount of force (in pounds per square inch) required to break through the side of a box. The rating is very straight forward - Burst Strength is measured in pounds per square inch. Generally, an ECT 32 box will have a burst strength of 200 lbs. Double-wall corrugated boxes can have a burst strength of up to 600 lbs (ECT 82), and triple-wall boxes up to 1300 lbs (ECT 112)
|
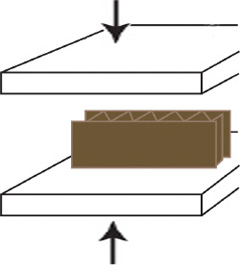
The Edge Crush Test
|
RECYCLING CARDBOARD
|
 |
One advantage to using corrugated cardboard for boxes or other packaging protection is that it can easily be recycled and remade into boxes again or other post-consumer material. Alternately, a special "Corrugated Shredder" may be purchased by manufacturers or those who order the boxes. This machine shreds the cardboard into a soft material that can be used as protective padding or cushioning.
Used cardboard can easily be compressed and tightly packaged for low-cost shipping to the recycling facility. Once there, it is placed in a hydropulper, which is essentially a large container of warm water. This machine cleans and breaks up the cardboard, turning it into a masticated material called pulp slurry.
The machines used to reprocess the cardboard can remove all kinds of unwanted debris, including twine and other straps, metal staples, and adhesives. Once it is pure paper pulp again, it can go back into the cycle to become kraft paper once again.
|
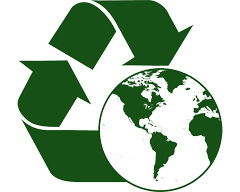
|
|
KEENART MEDIA CARDBOARD BOXES
|
 |
At KeenART Media, we use corrugated cardboard every day. We receive large, 84 x 100 inch C flute sheets with an ECT of 32. Due to the nature of our business, we do not order pre-cut boxes. Instead, we custom cut and fold the box for each and every order. Using a large, vertical paper cutter, we cut two sheets - one a 1/2 inch larger on each dimension. These two sheets serve as the base box and the lid. We then use a special folding tool to crease the cardboard where it will be folder to form the sides.
Flaps are cut from the creased edges, and stapled with a heavy duty stapler. Since the box is made to fit the exact dimensions of the order, we do not require much excess packaging to fill any spaces. Rather, we wrap everything in foam sheeting, and use polystyrene corners on large picture frames. We may use some left over strips of cardboard to internally reinforce the corners of the box, or lay a flat sheet of cardboard over canvas prints to protect them from any cuts the box may receive in transit.
Once the contents are securely packed in the base box, the lid slides neatly on top. This gives two layers of protection on each side, and three layers on each corner. As such, our shipped orders are as securely packaged as possible.
For more information on our custom packaging procedures, take a look at our comprehensive How To: Custom Shipping Boxes.
|
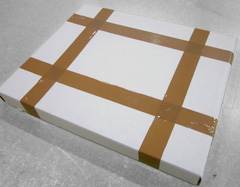
|
CARDBOARD AS ART
|
 |
As a practical shipping and storage too, corrugated cardboard can be the perfect solution. But its usefulness doesn't stop there. Over the last century, countless people have found ways to "recycle" cardboard boxes in their own way: by turning it into art!
In its simplest form, cardboard is a great surface on which to paint or draw. Unlike most paper, it is thick enough to keep markers from bleeding (out and through) and won't get soggy or rip beneath water-based paints. It is readily available, and as an inexpensive media, it can allow artists to create large pieces that would cost a fair bit on canvas.
Cardboard is also great for three dimensional art. It is rigid, but still relatively simply to cut and fold. Amazing sculptures and relief designs have been created using nothing more than cardboard and glue. And the wide range of flutes, colors, and thicknesses makes it easy to create almost anything at all.
Corrugated cardboard is not the only option for art. There is some incredible toilet paper roll art that makes the most of miniaturization. This eternally present material can also be cut and curled to create beautiful home decor, as well.
As always, Pinterest is home to a wealth of great ideas. Check out our cardboard art board - updated regularly - for tutorials and inspiration.
YouTube also has some great examples:
|
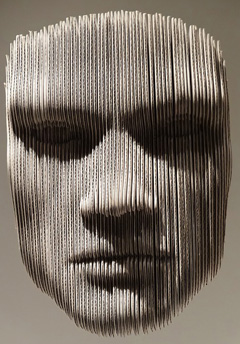
|
As you can see, corrugated cardboard has had a large impact on the commercial and private sectors. In a time of increased concern for sustainability, a shipping product that can be recycled and reused with relative ease is a significant tool.
If you have any questions about our shipping methods, products, or services, please do not hesitate to contact us. Our knowledgeable staff are always happy to answer your enquiries and provide suggestions or advice.
|
|

|
Custom-Made Picture Framing, Custom Stretcher Bar Frames
, Custom Artist Canvas, Custom Canvas Stretching, Canvas transfer & Dry Mounting Services
A division of USA On Canvas -
|
|
© 2002-2025 - KeenART Media Ltd.
|
|
|
|